The ONE MOTO Processes for Sustainable Manufacturing
and Assembly
Creating a sustainable manufacturing process for electric vehicle assembly is key to ensuring the benefits of EVs extend beyond just reducing emissions on the road, it is integral to our values. From sourcing materials to final assembly, we are transparent in our pledge and demonstrate this through building greener, more efficient
production lines.
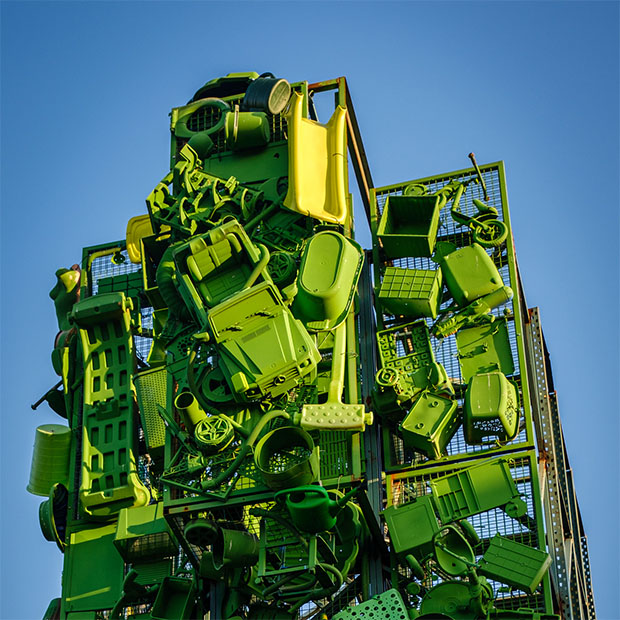
Sustainable Material Sourcing
Recycled, Recyclable and Renewable Materials
- Prioritising the use of recycled metals (aluminium, steel) and renewable materials (bioplastics, natural fibres) in vehicle components.
- Working with suppliers who have certified sustainable practices and traceable supply chains.
Minimising Rare Earth Materials
- Reducing reliance on rare earth elements by researching and adopting alternative materials and technologies, such as using synthetic graphite instead of natural graphite in batteries. As well as developing new forms of battery chemistry for the future of mobility.
Ethical Sourcing
- Ensuring all raw materials are sourced from suppliers who adhere to ethical labour practices and meeting our principle ESG framework (if they don’t have proprietary practices in place), focusing on reducing environmental impact and improving workers’ rights.
Energy-Efficient Manufacturing
Implement Renewable Energy Sources
- Powering the manufacturing facility with renewable energy (solar, wind, hydroelectric) to reduce the carbon footprint of production.
- Install energy-efficient lighting, heating, and cooling systems throughout the facility.
Using Energy-Efficient Equipment
- Investing in advanced machinery and robotics designed to minimise energy consumption.
- Regularly maintain equipment to ensure it operates at peak efficiency, preventing energy wastage.
- With automation in production being a focal point, creating jobs and increasing In-Country Value (ICV) where possible is crucial to our values.
Optimising Production Processes
- Implementing lean manufacturing techniques to reduce waste and streamline production.
- Utilising just-in-time production minimising the storage of excess materials and components, reducing waste and energy use.
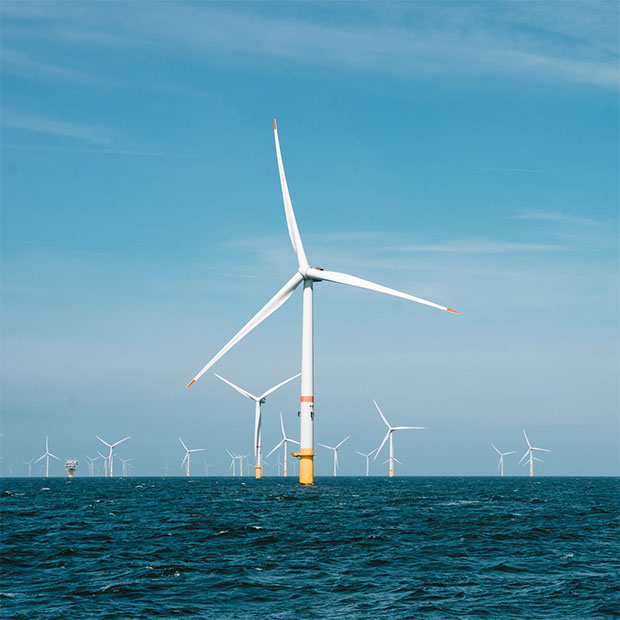
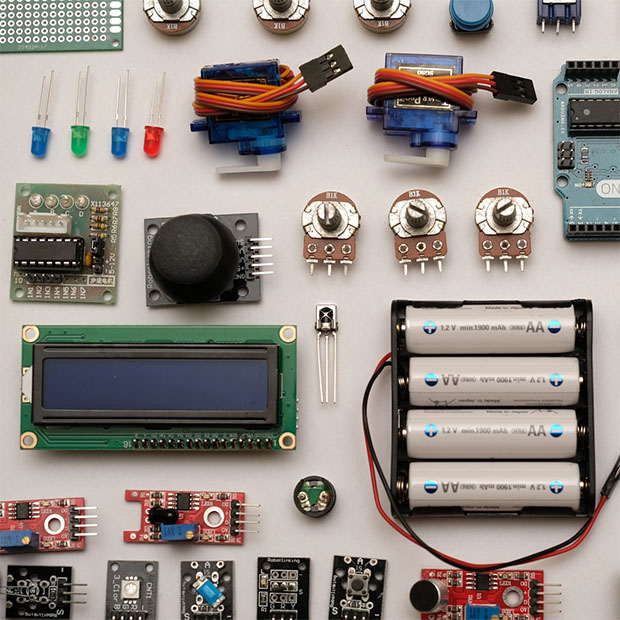
Waste Management and Recycling
Establishing a Zero-Waste Policy
- Aiming for zero waste by recycling scrap materials, reusing components, and reducing packaging.
- Setting up waste sorting stations to ensure that all recyclable materials are properly processed.
Closed-Loop Manufacturing
- Implementing closed-loop systems where waste materials from one process are reused in another, reducing the need for new raw materials.
- Encourage suppliers to adopt similar practices, creating a fully circular supply chain.
Battery Recycling (in development)
- We are looking to develop or partner with battery recycling programs to recover valuable materials from spent batteries, reducing the need for new mining activities.
Water Conservation
Water-Efficient Processes
- Use water-efficient technologies in manufacturing processes, such as closed-loop cooling systems and water recycling systems.
- Monitor water usage regularly to identify areas where consumption can be reduced.
Rainwater Harvesting (in development)
- Installing rainwater harvesting systems to capture and reuse rainwater for non-potable purposes, such as cooling and irrigation within the facility.
Wastewater Treatment (in development)
- To treat and recycle wastewater on-site to prevent contamination and reduce the demand for fresh water.
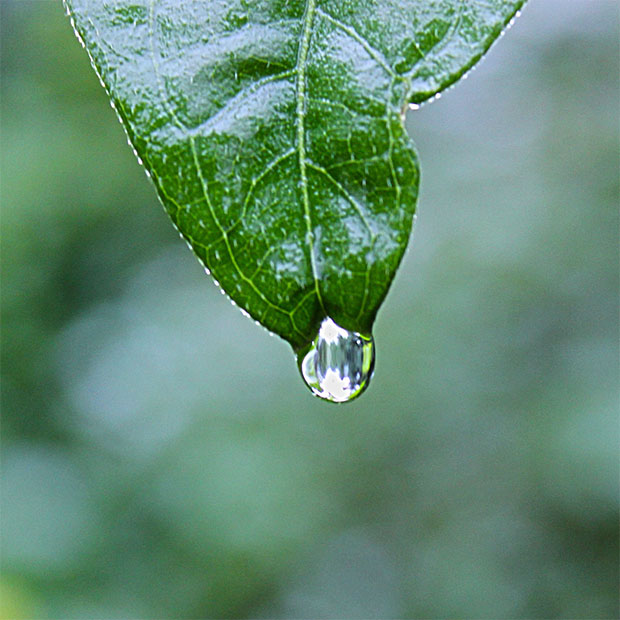
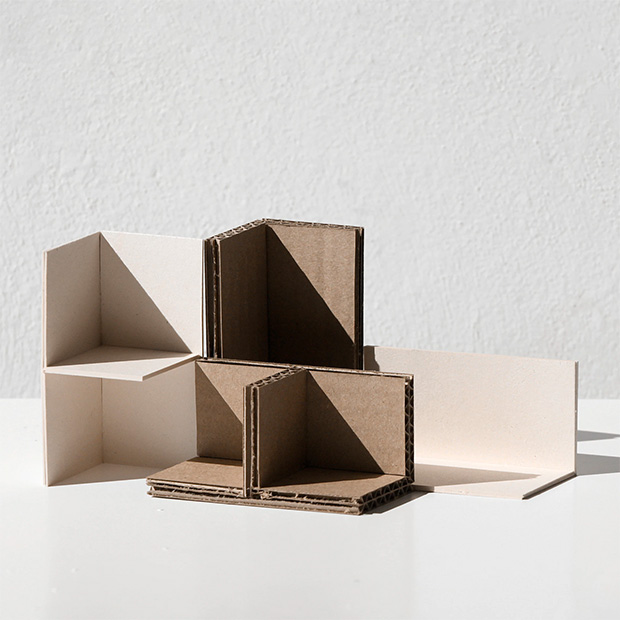
Sustainable Packaging
Use Eco-Friendly Packaging Materials
- Opting for packaging materials made from recycled content and that are recyclable or biodegradable. Currently more expensive, but to what expense if we didn’t?!
- Minimising packaging to reduce waste and material use.
Reusable Packaging Solutions
- Implementing reusable packaging systems for transporting components and finished products.
- Working with suppliers and distributors to standardise packaging sizes and materials to facilitate reuse.
Reduce Packaging Waste
- Design packaging with waste reduction in mind, eliminating unnecessary materials and space.
- Educate staff and suppliers on sustainable packaging practices.
Transportation and Logistics
Optimising Supply Chain Logistics
- Shorten supply chains by sourcing materials and components from local or regional suppliers when possible, reducing transportation emissions. Near-shoring production to the epicentre of local and regional sales and export.
- Using electric or low-emission vehicles for transporting materials and finished products where possible.
Efficient Transportation Planning
- Consolidating shipments and optimising delivery routes to minimise the number of trips needed, reducing fuel consumption and emissions.
- Adopting smart logistics management software to optimise load sizes and minimise empty runs through big data and AI.
Carbon Offset Programs
- Investing in developing carbon offset programs to compensate for any unavoidable emissions generated during transportation, production and end use.
- Developing carbon offset programs for our customers.
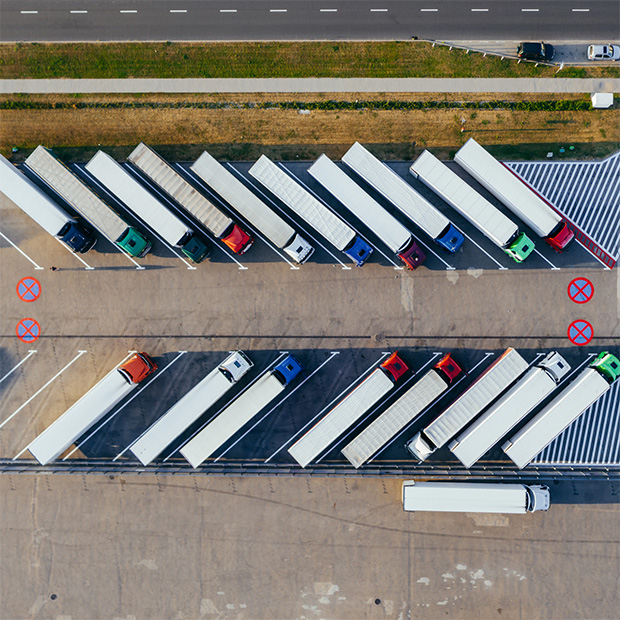
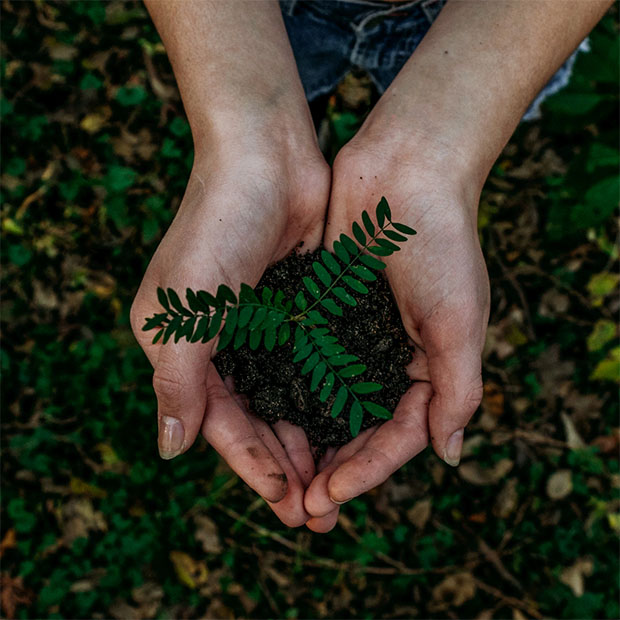
Employee Engagement and Training
Sustainability Training
- Providing training for employees on sustainable manufacturing practices, including energy conservation, waste management, and resource efficiency.
- Encouraging employees to contribute ideas for further improving sustainability in the manufacturing process.
- Empowering our teams to adopt sustainable practices and considerations in their private lives (commuting, household recycling, domestic use reduction)
Foster a Culture of Sustainability
- Creating initiatives involving employees in sustainability projects, such as energy-saving challenges or waste reduction competitions.
- Recognising and rewarding employees, partners and customers who contribute significantly to sustainability goals
Continuous Improvement
- Regularly reviewing and update sustainability practices based on the latest industry standards and innovations.
- Encouraging ongoing feedback from employees to expose areas for improvement
Lifecycle Assessment and Product Design
Conduct Lifecycle Assessments (LCA)
- Performing LCAs on all products to understand the environmental impact of each stage, from raw material extraction to end-of-life disposal.
- Use LCA data to inform product design decisions that minimise environmental impact.
Design for Durability and Recyclability
- Designing EV components for longevity, reducing the need for frequent replacements.
- Ensure that vehicles and batteries are easy to disassemble and recycle at the end of their life
Continuous Innovation
- Investing in R&D (and partnering with others) for more sustainable materials, manufacturing processes, and technologies.
- Remaining informed on the latest trends and developments in sustainable manufacturing to remain a leader in the industry.
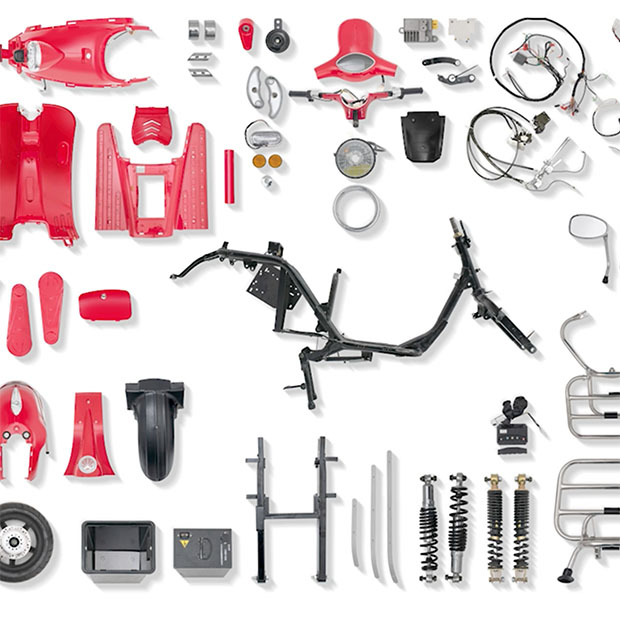
By following these steps, we are able to demonstrate our commitment towards “doing it right, doing it better” and it can create a sustainable, efficient, and forward-thinking production line not only supporting the growth of the electric vehicle industry but also support and maintain our global market position and brand equity.